Choose the Right Underlayment Material for Your Metal Roofing Project
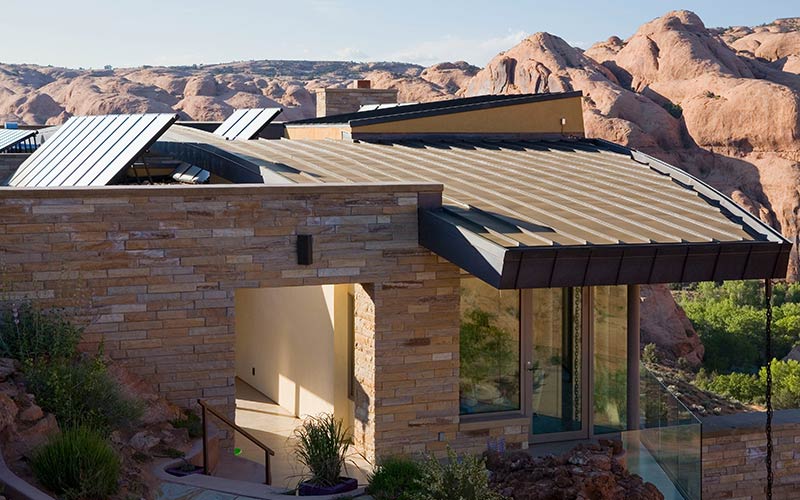
Roofing Underlayment Materials
Underlayment products for use beneath standing seam metal roof systems should be carefully selected to provide a roof system that performs optimally throughout the life of the building. Several considerations must be addressed in the roofing system design, including ensuring that the four barriers needed in any building enclosure i.e., water barrier, thermal insulation barrier, vapor retarder, and air barrier are provided and are in the correct location for a given climate.
Long term, in-service roof performance can be affected by several important factors including: the metal roofing system and its expected service life, the climate at the building location, roof slope and geometry, and ambient conditions (temperature/relative humidity) within the building. Improper selection of the roof underlayment may allow roof leakage or entrap moisture due to vapor diffusion or air exfiltration, which may accelerate deterioration of concealed components, shortening their service life and necessitating repairs. Further, to provide longevity the underlayment should match the intended service life of the metal roofing system.
Structural metal roof panel systems are designed to span structural supports without requiring a structural deck. Hence, they do not typically include roof underlayment since the installation lacks a continuous substrate or deck to support the underlayment material.
For architectural metal roof panel systems, a roof underlayment is required to help control water leakage through the roofing system during heavy rain storms or under snow melting conditions. Upgraded roof underlayment is often specified in cold climates for additional protection against ice dam leakage, while high temperature underlayments are designed for use in high temperature environments where the in-service temperature can reach temperatures as high as 240ºF.Typical underlayment materials include:
- (Asphalt-saturated) felt underlayment
- Synthetic sheet underlayment
- Rubberized asphalt or butyl-based sheet, with polyethylene facer, self-adhering membrane underlayment
Felt Underlayment
The traditional and most common material used for roof underlayment on a steep-slope metal roof is non-perforated, asphalt-impregnated felt underlayment. There are several types of felt underlayment including both organic reinforced and inorganic reinforced. Compared with organic reinforced felt underlayment, inorganic, glass-fiber- reinforced felt underlayment usually lies flatter and stands up better than the organic kind.
Depending on the demands of the architect, building code or the metal panel manufacturer, one or two layers of non-perforated asphalt felt are used local.
Felt underlayment provides little resistance to air and moisture vapor migration and does not serve as an effective air barrier. Architectural metal roofs with felt underlayment are best suited for buildings with proper slope and low moisture loads in dry or arid climates. Conversely, felt underlayment is appropriate in conjunction with ice dam protection at eaves and other critical transitions in cold climates.
Synthetic Sheet Underlayment
Synthetic plastic sheet underlayment are generally made of polyethylene, polyolefin, or polypropylene, between eight to 30 mils thick. Synthetic plastic sheet underlayment is less susceptible to wind damage, and lies flatter when subjected to wetting after installation. They are less sensitive to cold weather installation than felt and cost less than self-adhering membrane underlayment.
Most of the synthetic sheet underlayment sold is vapor resistant and generally do not qualify as air barriers.
Self-adhering Membrane Underlayment
Sheet membrane roof underlayment, consisting of either a rubberized-asphalt or butyl-based adhesive with a polyethylene carrier sheet, is a peel-and-stick product designed to adhere to the roof deck. They are effective on standing seam metal roofs for ice dam protection in the places you might expect including roof eaves, valleys, dormers, or rising walls. Conversely, when compared to asphalt-based membranes, butyl-based self-adhering sheet membranes provide protection in high temperature environments where the in-service temperature can reach temperatures as high as 240ºF. This is of particular importance for architectural metal roof assemblies because elevated roof surface temperatures, especially in desert climates and at high elevations, can exceed the melting point of some asphalt-based sheet membranes and damage the membrane.
These membranes are typically vapor impermeable and since they are fully-adhered to the substrate and to adjacent sheets at side and end laps, they resist air pressure differentials and serve as an effective air barrier material.
Choosing the proper and most effective underlayment for a metal roofing system will undoubtedly result in maximum roof performance and can play an important role in extending the life of the roof and of the building it protects.